Web Wire Mesh offers wire mesh in a wide range of meshes and materials. With efficient processing capabilities, we are able to customize our wire mesh to meet your needs. Please check the following processing capabilities for your reference.
Slitting
Our wire mesh is generally available in 36”, 48” and 60” wide rolls. Our custom designed Wire Mesh Slitting machines can handle virtually any slitting requirement.Cutting the wire mesh lengthways and rolling up to provide the exact width. Our equipment is capable of handling widths as small as 1/4 inches.
Cutting & Shearing
We can cut into straight dimensions or laser cut to a specific design pattern. For finer material, plasma cutting is available to flawlessly seal the edge of the wire mesh. The wire mesh can also be cut into complete circles in varying sizes. In addition, they can also be shear cut on a 45-degree bias that finishes with a square diamond pattern.
Welding
We also maintains a full-range of welding machinery in order to effectively meet the demands of a wide array of industrial users. .We have extensive capabilities to assemble smaller filtration and separation components using automated spot, seam, and circumferential resistance welding processes. Larger filters and other components are manufactured using TIG, MIG, and Laser welding capabilities.
Flattening
Web Wire Mesh offers a flattening service for cut-to-size pieces. With special, in house machinery known as rollers, we are able to flatten and ship almost any wire mesh.
Punching
Web Wire Mesh can effectively handle all of your punching needs. Our fabricating technicians have the expertise and tooling to deliver a quality product as per your exact specifications. Web Wire Mesh excels at punching both woven and welded wire mesh.
Forming
Our Press and Apron Brake machines can bend material to your specification.These machines are also used in our edging production to bend metal stock to create our ever-popular hooked screens often use for sizing and sifting in vibratory equipment.
Edging
Web Wire Mesh offers several edging options that include hooked, metal, canvas etc. Hooked screens are fabricated with quality metal strips using one of our press brakes. For metal bound edging like our infill panels, metal stock is used to form a channel to surround the perimeter of the mesh insert then pressed firmly into place using our press brake once again.
Rolling & Straightening
For more ridged and course meshes, our rolling machines allow us the ability to straighten out material that may have a slight cast or curve due a previous coiled state. Alternatively, these machines also help to re-roll the mesh with consistent tension for staging and shipping purposes. Material can also be formed to create partial or complete cylinders using this equipment as well.
Cleaning
Many customers require us to remove oils, dirt, or debris from their wire mesh. We offer a wide variety of cleaning methods such as vapor degreasing, ultrasonic, aqueous, or thermal cleaning.
Calendering
Calendering flattens the wire and reduces the thickness providing a uniform and precise material thickness throughout the mesh. This is used for applications where a controlled thickness is necessary. This process also increases the stability of the woven wire mesh.
Annealing
Annealing improves ductility enhancing the formability of wire mesh . Annealing will remove the stresses created in the wire drawing and weaving processes with a full anneal or stress relief based on your specific requirements.
Sintering
Sintering creates a metallurgical bond between the wires in our high temperature and controlled atmosphere ovens. This treatment can improve wire cloth rigidity, conductivity, and reduce fraying. This process can be done with a single layer of wire cloth, or multiple layers of wires cloth and other porous metal media (sometimes referred to as laminating).
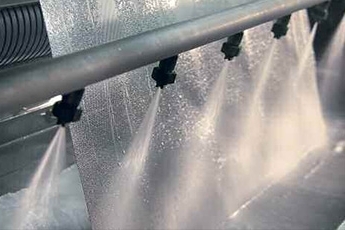
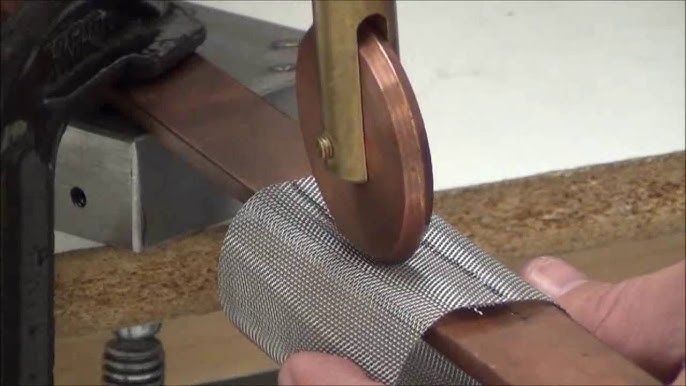
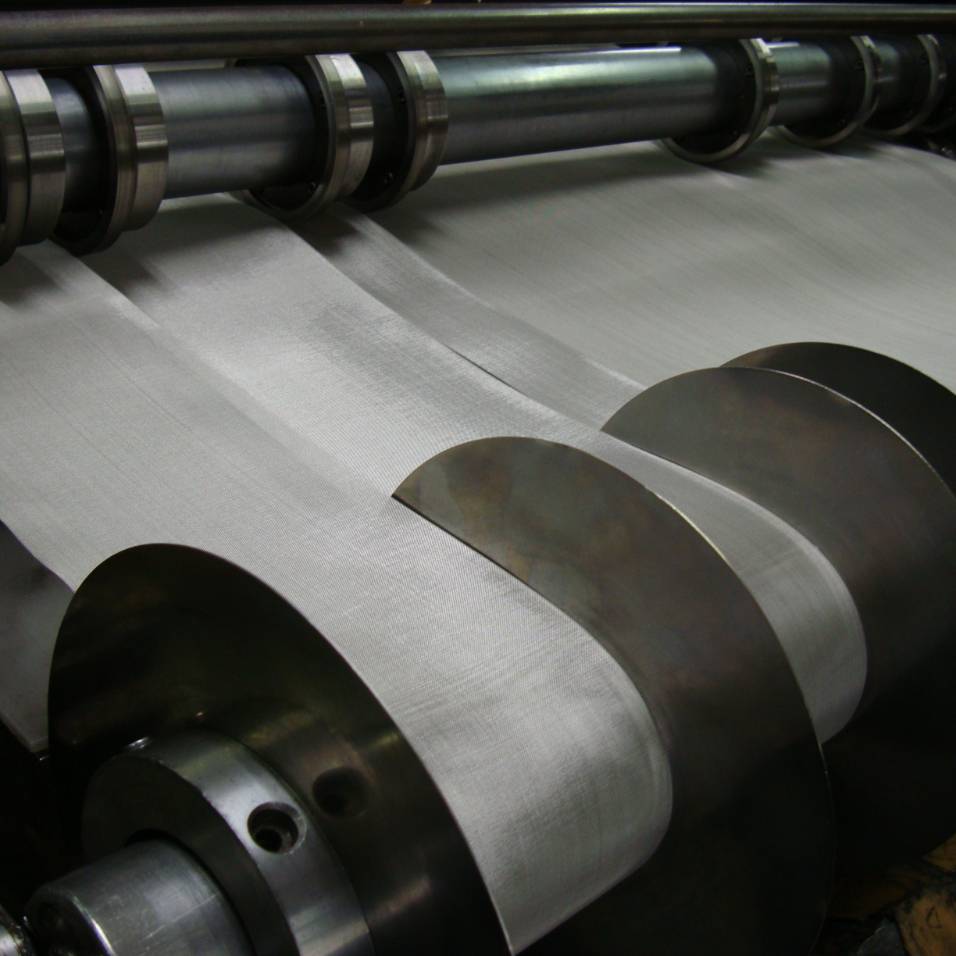
Leave a Reply